В днешния свят има три вида плоско стъкло: плоско изтегляне, флоатен метод и каландриране. Флоатното стъкло, което представлява повече от 90% от общото производство на стъкло в момента, е основният строителен материал в световното архитектурно стъкло. Процесът на производство на флоатно стъкло е основан през 1952 г., което поставя световния стандарт за висококачествено производство на стъкло. Процесът на флоатно стъкло включва пет основни стъпки:
● съставки
● топене
● формоване и покритие
● отгряване
● рязане и опаковане
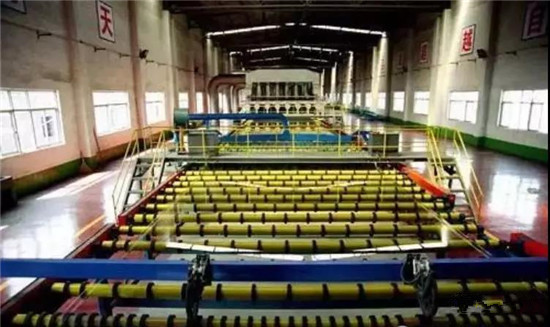
Съставки
Дозирането е първият етап, който подготвя суровините за топене. Суровините включват пясък, доломит, варовик, калцинирана сода и мирабилит, които се транспортират с камион или влак. Тези суровини се съхраняват в помещението за дозиране. В помещението за материали има силози, бункери, конвейерни ленти, улеи, прахоуловители и необходими системи за управление, които контролират транспортирането на суровините и смесването на смесените материали. От момента, в който суровините бъдат доставени в помещението за материали, те непрекъснато се движат.
Вътре в помещението за дозиране, дълга плоска конвейерна лента непрекъснато транспортира суровини от силозите с различни суровини до кофовия елеватор, слой по слой, по ред, и след това ги изпраща до устройството за претегляне, за да се провери тяхното общо тегло. Към тези съставки се добавят фрагменти от рециклирано стъкло или върнати продукти от производствената линия. Всяка партида съдържа около 10-30% счупено стъкло. Сухите материали се добавят в смесителя и се смесват с партидата. Смесената партида се изпраща от помещението за дозиране до силоза на пещта за съхранение чрез конвейерната лента и след това се добавя в пещта с контролирана скорост от подаващото устройство.

Типичен състав на стъклото
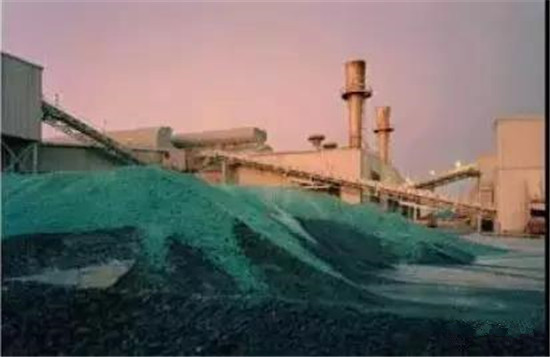
Двор за трошки
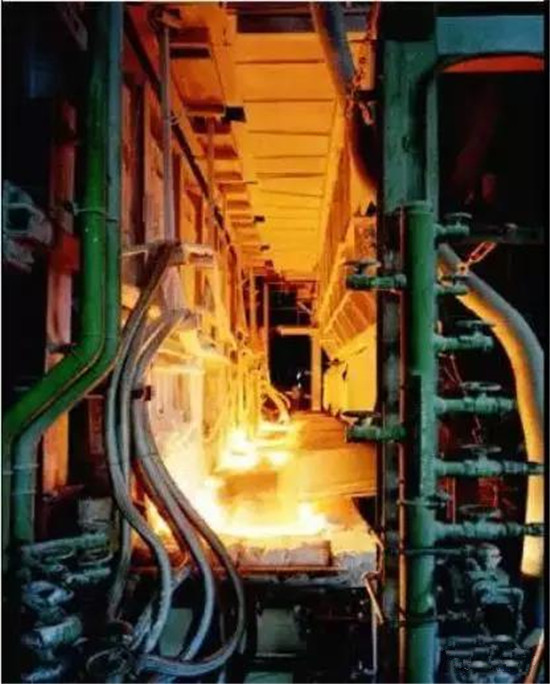
Подавайте смесените суровини във входа на пещта до 1650 градуса с бункер
Топене
Типичната пещ е пещ с напречен пламък и шест регенератора, широка около 25 метра и широка 62 метра, с дневен производствен капацитет от 500 тона. Основните части на пещта са топилна вана/утаител, работна вана, регенератор и малка пещ. Както е показано на Фигура 4, тя е изработена от специални огнеупорни материали и има стоманена конструкция на външната рамка. Шахтата се изпраща към топилната вана на пещта чрез захранващото устройство, а топилната вана се нагрява до 1650 ℃ от пистолет за пръскане с природен газ.
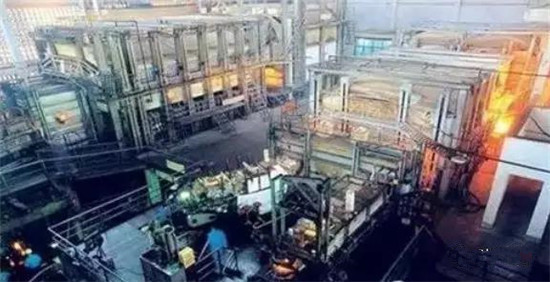
Разтопеното стъкло преминава от топилната вана към областта на гърлото през избистрителя и се разбърква равномерно. След това се влива в работната част и бавно се охлажда до около 1100 градуса, за да достигне правилния вискозитет, преди да достигне калаената вана.
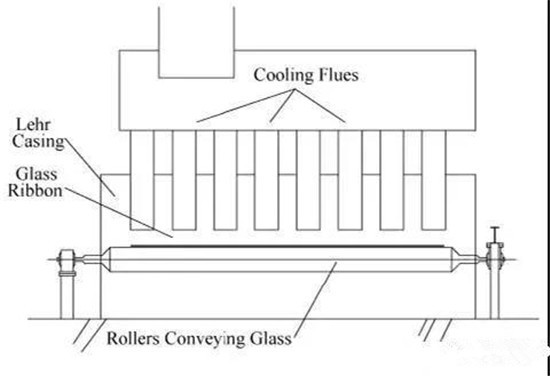
Формоване и покритие
Процесът на оформяне на избистреното течно стъкло в стъклена плоча е процес на механична манипулация, съобразен с естествената тенденция на материала, а естествената дебелина на този материал е 6,88 мм. Течното стъкло изтича от пещта през каналната зона и потокът му се контролира от регулируема врата, наречена рам, която е на около ± 0,15 мм дълбочина в течното стъкло. То плува върху разтопен калай - оттук и името флоат стъкло. Стъклото и калайът не реагират помежду си и могат да бъдат разделени; взаимното им съпротивление в молекулярна форма прави стъклото по-гладко.
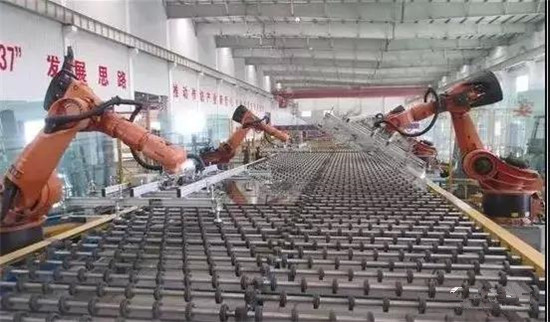
Ваната е запечатана в контролирана азотно-водородна атмосфера. Тя включва носеща стомана, горен и долен корпус, огнеупорни материали, калай и нагревателни елементи, редукционна атмосфера, температурни сензори, компютърна система за управление на процеса, с ширина около 8 метра и дължина 60 метра, а скоростта на производствената линия може да достигне 25 метра в минута. Калайната вана съдържа близо 200 тона чист калай, със средна температура от 800 ℃. Когато стъклото образува тънък слой в края на входа на калайната вана, то се нарича стъклена плоча и от двете страни работят серия от регулируеми издърпвачи на ръбове. Операторът използва управляващата програма, за да настрои скоростта на пещта за отгряване и машината за изтегляне на ръбове. Дебелината на стъклената плоча може да бъде между 0,55 и 25 мм. Горният нагревателен елемент се използва за контрол на температурата на стъклото. Тъй като стъклената плоча непрекъснато протича през калайната вана, температурата на стъклената плоча постепенно ще спада, правейки стъклото плоско и успоредно. В този момент, acuracoat може да се използва ® за онлайн покритие на отразяващо фолио, нискоемисионно фолио, фолио за соларно регулиране, фотоволтаично фолио и самопочистващо се фолио върху пиролизно CVD оборудване. В този момент стъклото е готово за охлаждане.
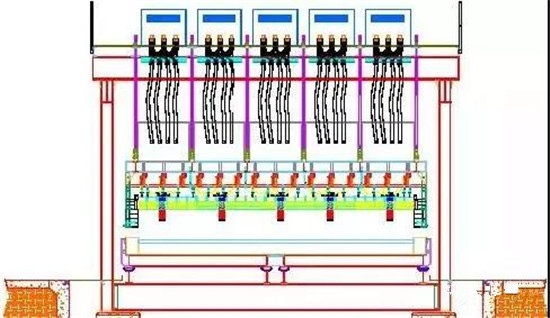
Напречно сечение на банята
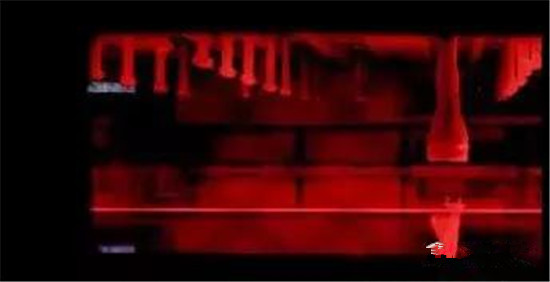
Стъклото се разстила на тънък слой върху разтопения калай, държи се отделно от калая и се оформя в чиния.
Висящият нагревателен елемент осигурява подаване на топлина, а ширината и дебелината на стъклото се контролират от скоростта и ъгъла на издърпвача на ръбове.
Отгряване
Когато оформеното стъкло напусне калаената баня, температурата на стъклото е 600 ℃. Ако стъклената плоча се охлади в атмосферата, повърхността на стъклото ще се охлади по-бързо от вътрешността на стъклото, което ще доведе до сериозно компресиране на повърхността и вредно вътрешно напрежение в стъклената плоча.
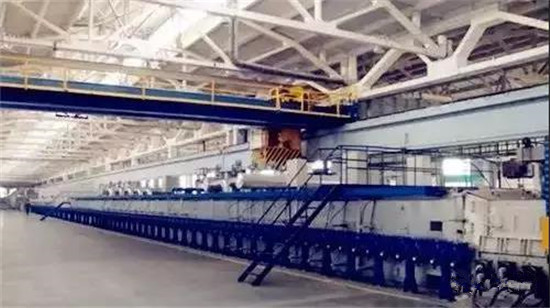
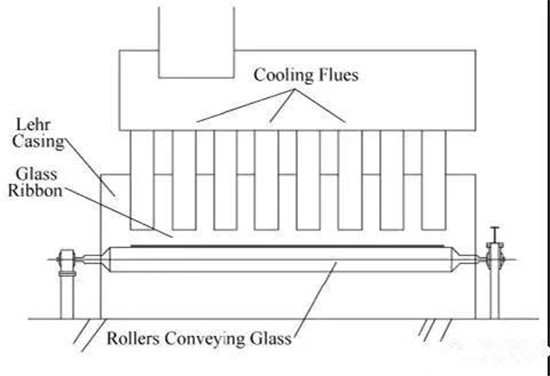
Секция от пещ за отгряване
Процесът на нагряване на стъклото преди и след формоването е и процес на образуване на вътрешно напрежение. Следователно е необходимо да се контролира топлината, за да се намали постепенно температурата на стъклото до околната температура, т.е. отгряването се извършва в предварително зададена температурна градиентна пещ за отгряване (виж Фигура 7) с ширина около 6 метра и дължина 120 метра. Пещта за отгряване включва електрически контролирани нагревателни елементи и вентилатори, за да се поддържа стабилно напречното разпределение на температурата на стъклените плочи.
Резултатът от процеса на отгряване е, че стъклото се охлажда внимателно до стайна температура без временно напрежение или напрежение.
Рязане и опаковане
Стъклените плочи, охладени от пещта за отгряване, се транспортират до зоната за рязане чрез ролкова маса, свързана със задвижващата система на пещта за отгряване. Стъклото преминава през онлайн система за проверка, за да се отстранят евентуални дефекти, и се реже с диамантен режещ диск, за да се отстрани ръбът на стъклото (материалът на ръба се рециклира като счупено стъкло). След това се нарязва на размер, изискван от клиента. Повърхността на стъклото се поръсва с прахообразен материал, така че стъклените плочи да могат да се подреждат и съхраняват, за да се избегне слепване или надраскване. След това безупречните стъклени плочи се разделят на купчини за опаковане с ръчни или автоматични машини и се прехвърлят в склада за съхранение или изпращане до клиентите.
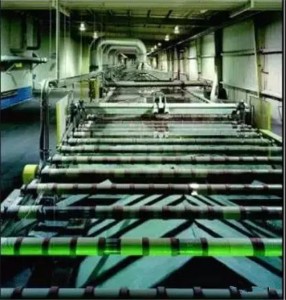
След като стъклената плоча напусне пещта за отгряване, тя се оформя напълно и се премества в зоната за охлаждане, за да продължи да намалява температурата.